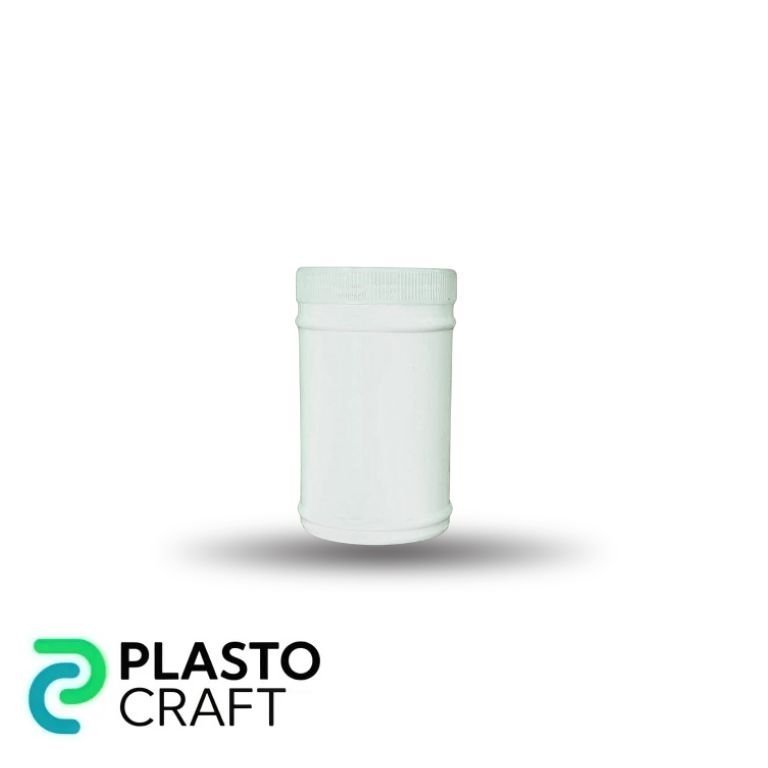
HDPE Injection Jars
Â
Specification | Detail |
---|---|
Capacity | 500 Grams |
Height | 5.5 Inches |
Ground Diameter | 14 Inches |
Minimum Order Quantity 500
DESCRIPTION
Packaging is a crucial aspect of product distribution, ensuring safety, preservation, and presentation. Among the various packaging materials available, HDPE (High-Density Polyethylene) stands out for its exceptional durability, chemical resistance, and recyclability. The HDPE injection jar, made using an injection molding process, is a highly regarded packaging solution that embodies these qualities. In this article, we will delve into the features, advantages, applications, and environmental impact of HDPE injection jars, highlighting why they have become a preferred choice in the modern packaging industry.
Understanding HDPE Injection Jars
HDPE injection jars are containers manufactured using the injection molding process, a versatile and precise technique for shaping plastic materials. The jars are crafted from high-density polyethylene, a thermoplastic known for its strength, impact resistance, and chemical stability. The injection molding process ensures consistent and high-quality jar production with enhanced design flexibility.
The Injection Molding Process
Injection molding is a manufacturing process wherein molten plastic is injected into a mold cavity under high pressure. Once the plastic cools and solidifies, the mold opens, and the finished product is ejected.
Advantages of Injection Molding:
– High production efficiency
– Precise and complex designs
– Minimal material waste
– Consistent product quality
Advantages of HDPE Injection Jars
Durability and Impact Resistance:
HDPE is renowned for its durability and resistance to impact, ensuring the jars withstand rough handling during transportation and storage.
Chemical Resistance:
These injection jars exhibit excellent chemical resistance, making them suitable for packaging a wide range of products, including food, pharmaceuticals, and household chemicals.
Design Versatility:
The injection molding process allows for intricate designs, enabling manufacturers to customize HDPE jars to meet specific branding and product requirements.
Lightweight:
Despite their sturdiness, Injection jars are relatively lightweight, reducing transportation costs and environmental impact.
Recyclability:
HDPE is one of the most widely recycled plastics, contributing to a more sustainable packaging ecosystem.
Applications of HDPE Injection Jars
Food and Beverage Industry:
HDPE jars are commonly used in the food and beverage sector to package items such as sauces, dressings, condiments, spices, and spreads. The durability and chemical resistance of HDPE ensure the products remain fresh and uncontaminated.
Pharmaceutical and Healthcare Products:
The superior performance of HDPE injection jar makes them ideal for packaging pharmaceuticals, vitamins, supplements, creams, and ointments. The jars’ chemical resistance ensures product efficacy and integrity.
Personal Care and Cosmetics:
HDPE injection jars find applications in the personal care and cosmetics industry for packaging creams, lotions, gels, balms, and beauty products. The injection molding process allows for precise design elements and branding.
Household and Cleaning Products:
Manufacturers of household cleaning products, such as detergents, cleaning agents, and surface cleaners, benefit from the durability and secure closure of HDPE injection jar.
Environmental Considerations
Recycling Initiatives:
HDPE is highly recyclable, and proper waste management and recycling initiatives are crucial for responsible plastic usage.
Sustainable Sourcing:
Using recycled HDPE or exploring bio-based alternatives can further reduce the environmental impact of HDPE injection jars.
Consumer Education:
Educating consumers about the importance of recycling and responsible plastic usage can promote environmentally-conscious behaviors.
Challenges and Sustainable Solutions
HDPE injection jars are containers meticulously molded from high-density polyethylene using an injection molding process. This method involves melting the HDPE resin and injecting it into a mold, resulting in a seamless, single-piece jar design. The technique provides intricate detailing, uniform thickness, and consistent quality, ensuring that every jar meets the highest standards.
Understanding HDPE Injection Jar
Single-Use Plastics:
While HDPE injection jars are recyclable, the challenge of single-use plastics persists. Manufacturers can explore reusable or refillable options to reduce waste.
Biodegradable Alternatives:
Continued research and development in biodegradable plastics offer a potential solution to reduce the environmental impact of traditional HDPE jars.
Eco-Friendly Packaging Materials:
Using eco-friendly materials for secondary packaging, such as labels and caps, can complement the sustainability of HDPE injection jars.
HDPE injection jars offer an excellent packaging solution that combines durability, design versatility, and environmental sustainability. The injection molding process ensures precise and consistent production, making HDPE jars suitable for various industries, from food and beverages to pharmaceuticals and personal care products.
As environmental concerns continue to grow, the packaging industry must prioritize sustainable practices and responsible plastic usage. By embracing HDPE injection jar and adopting eco-friendly initiatives, businesses can enhance consumer trust, product integrity, and contribute to a cleaner, greener, and more sustainable future.
With a focus on innovation and environmental stewardship, the future of packaging looks promising, striking a balance between functionality and environmental preservation. By collaborating with consumers, manufacturers, and recycling facilities, the packaging industry can pave the way towards a more sustainable and responsible packaging ecosystem.